Con la trigenerazione di AB, Perugina migliora l’efficienza energetica
Grazie alla recente installazione del nuovo impianto di trigenerazione di AB presso lo Stabilimento Perugina di San Sisto (PG), il Gruppo Nestlé ha compiuto un ulteriore passo avanti verso un utilizzo sempre più efficiente dell’energia.
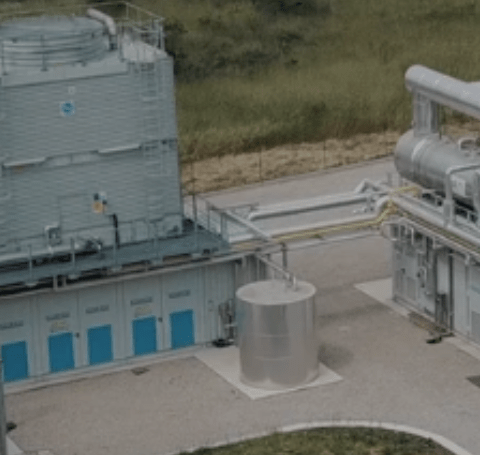
Grazie alla recente installazione del nuovo impianto di trigenerazione di AB presso lo Stabilimento Perugina di San Sisto (PG), il Gruppo Nestlé ha compiuto un ulteriore passo avanti verso un utilizzo sempre più efficiente dell’energia. L’impianto di AB è stato installato nello Stabilimento Perugina a fine 2020 in sostituzione di un precedente impianto di trigenerazione che ha smesso di essere operativo dopo oltre 15 anni.
Il trigeneratore installato è costituito da due gruppi di potenza elettrica 3.3 MW e 2.7 MW. Ciascun gruppo è composto da un motore endotermico alimentato a metano che muove un alternatore per generare energia elettrica. Il calore del motore e dei fumi, attraverso degli scambiatori, produce vapore e acqua calda. È presente anche un assorbitore che sfrutta l’energia termica residua per produrre acqua refrigerata. L’impianto lavora 24 ore su 24 e il regime dei motori può essere regolato in modo che l’energia prodotta sommata a quella del fotovoltaico siano istante per istante uguali al fabbisogno del sito.
Grazie all’energia termica prodotta dal trigeneratore di AB, i generatori di vapore lavorano per una minima parte, solo per mantenere costante la pressione del vapore nella rete. L’energia termica che viene sfruttata arriva a 3.5 MW e questo evita di bruciare fino a 400 mc di gas metano ogni ora. In pratica, ogni quattro ore, viene risparmiato il metano consumato da una famiglia media in un anno.
Questo, unito a miglioramento dell’efficienza energetica, alla produzione di energia elettrica con fotovoltaico e al fatto che l’energia elettrica acquistata dalla rete derivi da fonti rinnovabili, ha permesso allo stabilimento di San Sisto di abbattere le emissioni di CO2 in atmosfera del 30% in 5 anni, ottenendo un risparmio medio di 2.400 tons l’anno rispetto alle emissioni 2016.
Come testimonia la recente installazione del nuovo impianto di trigenerazione di AB, un elemento che caratterizza lo Stabilimento di San Sisto è l’attenzione all’impatto ambientale. Negli ultimi 5 anni infatti le emissioni di CO2 per tonnellata prodotta sono calate del 37%; inoltre è stato ridotto il consumo energetico per tonnellata prodotta del 36% e quello di acqua del 53%. Tra le iniziative che hanno permesso di raggiungere questi risultati: l’impianto fotovoltaico presente nel parcheggio e sul tetto fornisce 1.2 MW di picco, il riutilizzo dell’acqua nelle torri evaporative e l’ottimizzazione dell’energia per il condizionamento che è l’utenza più “energivora” del sito. Inoltre, nel 2016, è stato raggiunto l’obiettivo di Zero Waste for Disposal, avviando a riciclo o a valorizzazione oltre il 90% dei rifiuti prodotti nel sito produttivo.