Eural Gnutti e l’alluminio. La sfida bresciana
Eural Gnutti è specializzata nella produzione di semilavorati in leghe di alluminio. Al primo posto, a livello mondiale, per le barre trafilate e tra i maggiori produttori europei di barre estruse e profilati
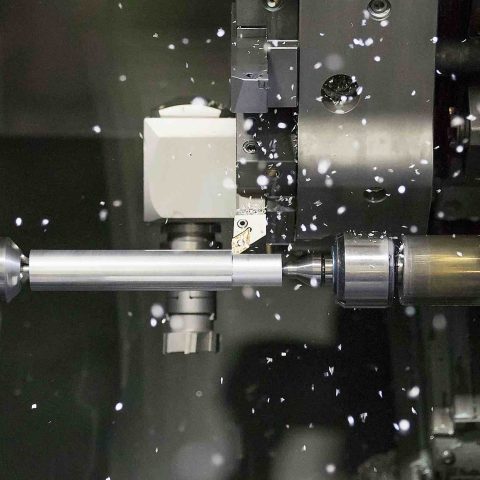
L’alluminio è un elemento pivotale anche nell’agenda di costruttori di motori e batterie, e quelli di Eural lo sanno. Questione di leggerezza e di resistenza alle temperature (vale anche per i raccordi di Eaton e gli scambiatori di calore di UFI FIlters). La famiglia Gnutti rilancia le quotazioni dell’acciaio made in Italy, sfidando i colossi eurasiatici, dai due stabilimenti ubicati nella bassa bresciana e ai piedi della Franciacorta.
I bracci operativi di Eural Gnutti. Una guida alla produzione
La fonderia di Pontevico, dove sono attive due linee di colata costitute da un forno fusorio a doppia camera e forni di attesa, assicura forniture di billette (semilavorati in forma di sbarra a sezione quadrata o rettangolare), dagli elevati e costanti standard, per l’impianto di estrusione e trafilatura di Rovato. Quest’ultimo integra tre fasi produttive: estrusione, con cinque linee che includono tre presse inverse per le barre e due presse dirette per i profili, trafilatura e trattamento termicoi. La presenza di una fonderia interna collegata all’impianto di estrusione consente a Eural Gnutti di offrire ai clienti un’omogeneità tra le diverse colate nel lungo termine. La gestione autonoma della fusione favorisce un maggiore impiego di alluminio riciclato. Nel 2023 la produzione di billette costituite al 74% da materiale riciclato, di cui 47% pre consumer (sfridi) e 27% post consumer (rottami) e un 26% di alluminio primario, I processi produttivi di Eural Gnutti si affidano a un sistema informativo integrato, che consente una costante sinergia tra i due stabilimenti e di impostare e monitorare le lavorazioni da remoto.
A Pontevico, per chi non fosse pratico di billette
In fonderia, a Pontevico, il materiale in ingresso è sottoposto a controlli in accettazione e nello specifico: controllo radiometrico per garantire l’assenza di contaminazioni radioattive, controllo visivo e analisi chimica per classificare la tipologia di materiale in accettazione. Prima di avviare la colata, si susseguono diverse fasi tra cui: preparazione, con la messa in forno fusorio dei materiali grezzi e rottami, alligazione volta ad ottenere ristretti range analitici per ogni elemento chimico. Durante la fase di colata, i parametri necessari per la solidificazione sono monitorati continuamente, al fine di ottenere una struttura cristallina omogenea. Successivamente, ogni billetta viene sottoposta a un’ispezione a ultrasuoni per garantire l’assenza di discontinuità interne, cricche, inclusioni o vuoti, in conformità ai requisiti di classe “A” della norma SAE AMS-STD-2154 (Tipo I), standard tecnico sviluppato dalla Society of Automotive Engineers (SAE) per la valutazione e il controllo qualità dei materiali metallici utilizzati in ambito aerospaziale e automobilistico. In aggiunta, per ogni colata è prevista l’esecuzione di un esame macrografico: una fetta di billetta viene aggredita chimicamente per rilevare la distribuzione della struttura cristallina. La garanzia di una struttura omogenea con una distribuzione regolare dei grani cristallini previene l’insorgenza di problemi di lavorabilità nell’impianto di Rovato. Infine, sia le colate che le billette sono identificate con un codice univoco a tracciabilità del lotto, della distinta materiali e delle pesate.
E a Rovato, per chi non ne sapesse mezza di scattivatura
A Rovato, i controlli e le verifiche di conformità sui prodotti vengono eseguiti dal reparto Qualità in accordo con gli standard interni, le normative di riferimento e i requisiti specifici dei clienti. In dettaglio, di routine vengono eseguiti per ogni lotto di produzione i seguenti test:
- Test di conducibilità termica su ogni pezzo, al fine di rispettare i requisiti di norma, ove applicabili e in generale verificare l’uniformità del lotto di produzione
- Test di trazione e durezza secondo gli standard internazionali
- Crash test e test di scattivatura per profili porthole su ogni colpo di estrusione, per verificarne l’integrità strutturale e la resistenza meccanica secondo standard interni di riferimento definiti da Eural Gnutti
- Test di analisi chimica di prodotto, in accordo con gli standard internazionali
- Test macrografico per verificare e classificare la struttura e l’uniformità della stessa agli standard interni, definiti da Eural Gnutti o da requisiti specifici del cliente
- Test di truciolabilità per verificare il grado di lavorabilità del materiale in accordo alla classificazione interna definita da Eural Gnutti, in base alla sua esperienza pluridecennale
- Test di rugosità per profili.
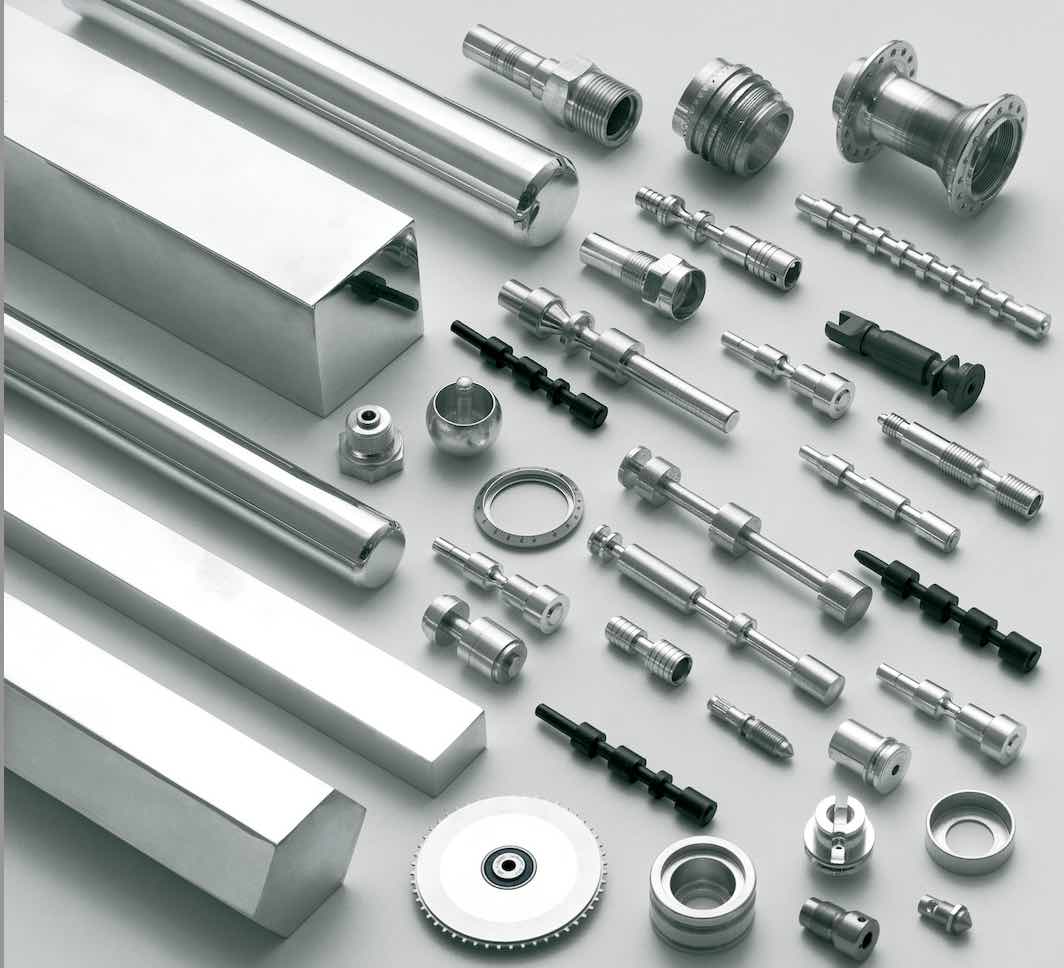