Flash Battery e l’orgoglio dell’assemblaggio ‘robotico’
Con oltre sei milioni di investimento Flash Battery ha espletato un passaggio fondamentale, con la linea automatizzata di assemblaggio moduli con saldatura laser
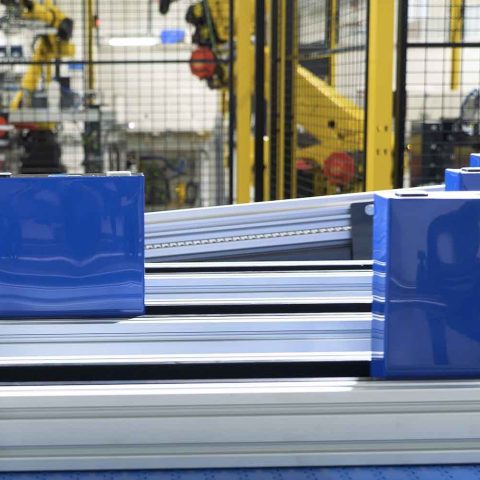
Flash Battery ha accelerato l’impronta domestica della transizione energetica. Cosa significa? La nuova linea automatizzata di assemblaggio moduli con saldatura laser è operativa presso il quartier generale di Sant’Ilario d’Enza. In merito alle ragioni delle brillanti performance di Flash Battery, il fondatore e ad, Marco Righi, ci ha risposto (ne trovate conferma sul numero di Marzo-Aprile di POWERTRAIN): «Facciamo tutto internamente, il che facilita l’aggiornamento continuo». E così, a quanto pare, sarà sempre di più.
Moduli con celle prismatiche
Sono più di sei i milioni di euro investiti per questo decisiva sterzata nella capacità produttiva, che si sviluppa su di una superficie pari a 2.200 metri quadri. Si tratta di un reparto progettato per ospitare l’intero processo di saldatura e integrazione meccanica in un ambiente controllato. La capacità annua raggiunge i 90.000 moduli, rendendo questa linea non solo la più avanzata ma anche la più produttiva in Italia per l’assemblaggio di moduli con celle prismatiche.
La virtuosa autarchia di Flash Battery
Riprendendo le parole di Marco Righi, Flash Battery ha scelto di conservare nel perimetro del proprio quartier generale le competenze chiave del processo: dal sistema di gestione proprietario, dal battery management system, alla progettazione meccanica ed elettrica, fino alla validazione dei processi e alla manutenzione predittiva. Con l’integrazione della nuova linea di assemblaggio moduli, l’azienda completa il processo di consolidamento produttivo interno, portando sotto il proprio diretto controllo anche le attività di saldatura e assemblaggio, fino ad ora affidate a fornitori esterni.
Le fasi produttive di un progetto dal respiro europeo
La linea di assemblaggio automatizzata è progettata per passare rapidamente da una configurazione all’altra, gestendo tredici varianti di moduli con tempi di cambio inferiori ai dieci minuti. Anche la saldatura laser rappresenta una scelta tecnologica strategica: garantisce giunzioni meccaniche ed elettriche più sicure, una maggiore resistenza alle vibrazioni e una minore dispersione energetica. È un passaggio fondamentale per ottenere prestazioni stabili e affidabili, soprattutto in applicazioni industriali soggette a sollecitazioni elevate. La linea opera secondo un processo articolato in quattro fasi fondamentali:
1. Carico e controllo automatizzato delle celle, tramite ispezione ottica e sensori di precisione;
2. Formazione del modulo, con stacking robotizzato e posizionamento dei componenti in una struttura di contenimento che verrà successivamente saldata;
3. Saldatura laser di frame e bus bar, che collegano le celle tra loro, per una connessione elettrica efficiente e duratura;
4. Test finali di conformità, inclusi controlli di sicurezza, isolamento e resistenza meccanica. Solo i moduli che superano i test vengono etichettati e asserviti nelle linee di assemblaggio dei pacchi batteria firmati Flash Battery.
In conclusione, le parole di Marco Righi, pronunciate per l’occasione: «Integrare le competenze produttive ci permette di rispondere con prontezza alle esigenze dei nostri clienti e sviluppare una proposta ad hoc ai massimi livelli di qualità e performance. Un vantaggio competitivo decisivo soprattutto in un mercato in costante evoluzione. Forti di questa autonomia produttiva, e con l’atteso avvio delle gigafactory europee dedicate alle celle LFP, saremo presto in grado di offrire ai nostri clienti una fornitura interamente europea».
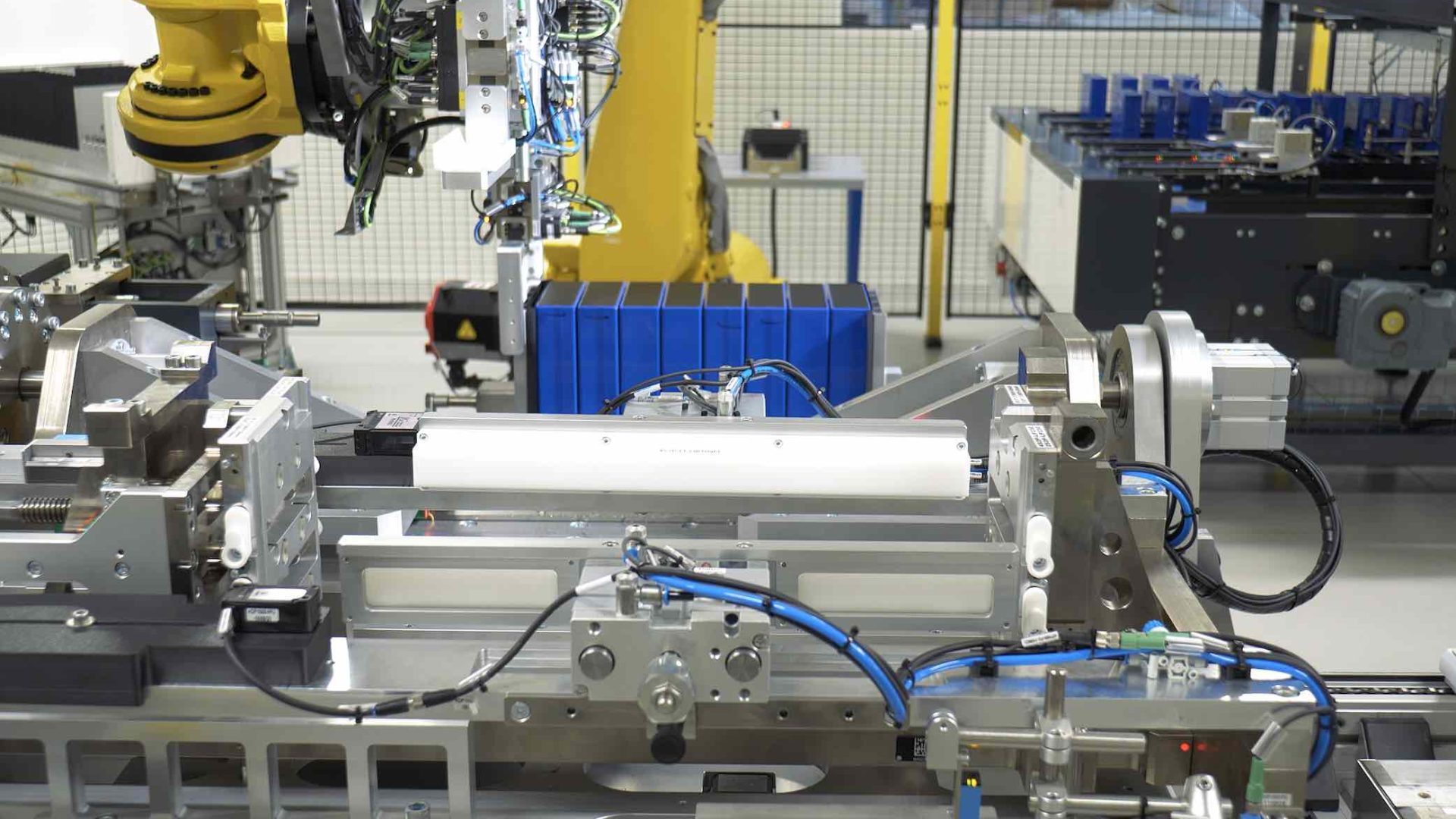