Flash Battery, enciclopedia industriale
Perché Flash Battery, intelligenza elettrica del Gruppo E80, non si limita a equipaggiare gli Agv della casa madre. Dalle piattaforme aeree ai telescopici, dalle macchine compatte da cantiere ai carri miscelatori, le batterie hanno superato la prova del nove. Il litio-ferro-fosfato se ne va alla conquista dell’industriale. Leggi l’articolo completo su Powertrain di marzo/aprile.
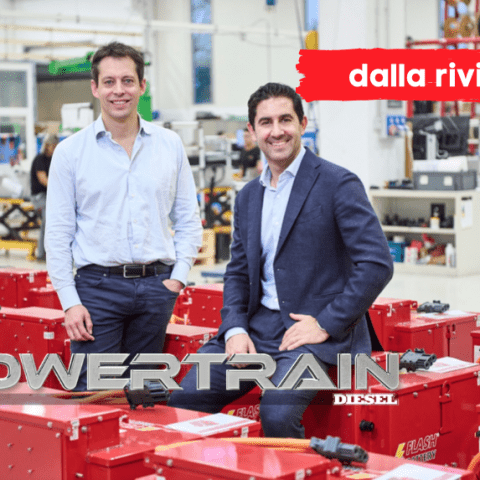
Bev, un acronimo che ha scosso nelle fondamenta l’ancien régime delle quattro ruote (Tesla è tallonata da una miriade di concorrenti cinesi, BYD su tutti. I marchi storici del design tedesco, invece, ancorati nella rada dell’endotermico e incagliati nella riconversione elettrica, sono alle prese con drammatici piani di ristrutturazione) e incombe nel conservativo anfiteatro delle applicazioni mobili industriali. Stazionari e marini non fanno eccezione, semmai si dimostrano ancor più recalcitranti alla conversione all’elettrico. Più o meno tutti gli attori della disfida della transizione sono stati folgorati sulla via del pacco batterie. La panoramica dei costruttori di accumulatori, assali e avviamenti elettrici, per lo meno alle latitudini occidentali, soffre l’asimmetria tra la pianificazione delle magnifiche sorti e progressive del phase-out endotermico e l’effettiva penetrazione del verbo elettrico nelle consuetudini e nella propensione degli utilizzatori finali. Il caso di Northvolt è esemplificativo, per non citare la teoria di start-up nel settore dei veicoli industriali (le montagne russe di Volta Trucks vi dicono nulla?).
Caccia allo specialista
Negli ultimi anni si è assistito all’accaparramento degli specialisti di batterie da parte di motoristi, Oem o altri attori del business industriale. La vicentina Sme è finita sotto l’ombrello di Dana nel 2019. Su questo numero vi raccontiamo anche la parabola di Archimede Energia, assorbita da HB4. Per focalizzarci sulla Motor Valley, anzi, restringendo ancora più il fuoco, sul distretto meccatronico reggiano, Benevelli è stata inglobata da Comer Industries. Zapi, che dell’elettrificazione è impregnata fin dall’atto fondativo, si è aggiudicata i servizi di solution provider di 4e Consulting.
C’è un’azienda, però, che sulla via Emilia, baricentrica tra Reggio e Parma, ha scritto un capitolo diverso di questa storia. Flash Battery, fondata da Marco Righi, che tuttora occupa il gradino più alto del management, si è imposta in questo scenario con una progressione lineare che l’ha scampata dalle lune traverse del mercato. E l’approdo in E80 Group protagonista assoluta dei veicoli a movimentazione automatica per i plessi manifatturieri, gli Agv, è risultato naturale e mutualmente vantaggioso. Ce lo conferma lo stesso Marco Righi: «In effetti, di produttori di batterie che sono riusciti a posizionarsi sul mercato, rimanendoci negli anni, ce ne sono sempre stati pochi. Alcuni, addirittura, sono falliti. Non è il caso di Flash Battery, che è cresciuta in modo armonico, camminando saldamente sulle sue gambe. E80 Group è entrata nel capitale con circa 400mila euro per rilevarne il 40%. Certo, lo sviluppo dell’elettrico si sta confermando lento, in uno scenario che si caratterizza per gli scarsi volumi e i grandi investimenti richiesti. Oltretutto, chi si aspetta volumi molti alti, spesso associati a prodotti standardizzati, deve fare i conti con il mercato asiatico. Inevitabile che costoro abbiano sofferto. Allargando lo sguardo, si vede una grande prospettiva per il futuro, i produttori di batterie sono di interesse globale, sia per la finanza che per l’industria. Lo dimostra il fatto che le acquisizioni non siano così facili, perché le aziende si fanno strapagare, anche quando non dispongono di una tecnologia consolidata».
Certo, questi specialisti sono una preda ghiotta per le aziende più strutturate, e spesso diventano captive.
«Si tratta essenzialmente di opportunità. I costruttori di powertrain tradizionali e gli Oem puntano a incorporare queste competenze. Per quanto ci riguarda, la collaborazione con E80 Group è partita nel 2013, l’ingresso nel capitale societario risale al 2015. È stata un’operazione a tutti gli effetti “win win”. Loro sono pionieri nell’utilizzo del litio e necessitavano di internalizzare le tecnologie, perché reduci da esperienze negative. La batteria è un elemento “sensibile”, in un impianto automatizzato con centinaia di carrelli a guida autonoma che funzionano senza sosta. Nel caso in cui una batteria abbia un’anomalia, questo rischia di inficiare la produttività dell’intero stabilimento. E80 Group ha così internalizzato il know-how e Flash Battery ne ha beneficiato in termini di volumi e competenze. La nostra è una logica diversa da quella che stanno recentemente seguendo i grandi gruppi nell’accaparrarsi i produttori di batterie, facendo un investimento in prospettiva. E80 Group ha intrapreso una politica di verticalizzazione per evitare qualsiasi rischio e confermarsi pioniera nell’elettrificazione della flotta al litio, rispetto ai concorrenti nel settore delle macchine automatiche».
Oltre quota 24mila
Mentre scriviamo, a Sant’Ilario d’Enza hanno appena sfondato il tetto delle 24.000 batterie confezionate, per circa 500 MWh prodotti. Torniamo da Righi.
«Flash Battery ha tre punti altamente distintivi: dispone del know-how e di un’elettronica proprietaria, brevettata. Il secondo aspetto importante, che deriva dal primo, è la capacità di customizzazione. Il terzo aspetto riguarda gli ulteriori sviluppi nel controllo da remoto. Sulla manutenzione predittiva stiamo lavorando molto e riteniamo rappresenti il futuro per fornire un prodotto di qualità. Flash Battery riesce a fornire risposte al cliente che non può rivedere il progetto della macchina adattandola alla batteria e richiede quindi un prodotto “tailor made”. Noi assicuriamo la consulenza durante la progettazione a interlocutori che frequentemente dispongono di profonde competenze nella parte endotermica e idraulica, ma hanno bisogno di essere accompagnati nella parte elettrica, in quanto ne stanno acquisendo di nuove. Prima del passaggio all’elettrico, i produttori non avevano idea di come le loro macchine venissero utilizzate e dei consumi effettivi. Adesso occorre dimensionare correttamente la batteria, perché altrimenti il veicolo costerebbe una follia e, per farlo, devi conoscere il modo in cui il cliente usa la macchina. Prima dell’entrata in vigore della 4.0 possiamo azzardare che il 95% delle macchine non fosse controllato in remoto. In fin dei conti, una volta che il serbatoio era vuoto, bastava riempirlo. Adesso è tutto più analitico, dovendo ragionare su risorse non infinite».
Come declinare le vostre competenze dall’assorbimento captive al progetto per una macchina operatrice?
«La consulenza iniziale è finalizzata alla comprensione del settore del cliente e del suo obiettivo, qual è la missione macchina, quali sono i consumi. Si determina il “pacchetto energia”, che comprende la batteria e il sistema di ricarica. La batteria può cambiare in funzione della capacità di ricarica del cliente. L’approccio è consulenziale e orientato a definire con precisione quali siano i consumi effettivi, esplorando il ciclo macchina al di là dei dati disponibili».
In merito alla vostra offerta, e non solo, di sistemi propulsivi Bev per applicazioni mobili industriali. Litio-ferro-fosfato unica via?
«Nella nostra offerta l’Lfp (litio-ferro-fosfato) è prevalente perché il nostro settore è quello dell’industria in generale, dal movimento terra al carrello elevatore alla macchina agricola. Il comune denominatore è che l’operatore utilizzi la macchina per diverse ore. Occorrono dunque batterie piuttosto grandi, per soddisfare le richieste più energivore, intorno alle due ore, fino alle sei/sette ore di utilizzo. La Lfp è la miglior chimica di energia, è competitiva perché non ha materiali critici all’interno, ha un costo inferiore e una sicurezza maggiore. Teniamo comunque gli occhi aperti su altre chimiche. Abbiamo delle preserie Nmc e al litio titanato, per assecondare le necessità degli installatori, vuoi per lo spazio a bordo macchina o per le potenze di utilizzo».
Del resto, il litio si caratterizza per l’intrinseco potenziale elettrochimico: una batteria agli ioni di litio genera da 2,4V ai 3,7V per elemento in funzione della chimica utilizzata. E il sodio?
«La tecnologia dei primordi, quella al sale fuso, è obsoleta, vincolata a temperature prossime ai 250 gradi, e non ha senso rispolverarla. Gli ioni di sodio sono tutt’altra cosa, con una resa elevata, talvolta superiore a determinate batterie al litio. Il loro limite è la scarsa densità, circa la metà dell’Lfp, e il livello di maturazione non ancora sufficiente per essere competitive. Hanno ricevuto una spinta forte negli anni scorsi, quando il prezzo del carbonato di litio era arrivato alle stelle. Ad oggi, con una quotazione del litio ai minimi storici, non ha minimamente senso, se non nell’ottica dell’energy storage, dove il volume è poco rilevante e potrebbero rappresentare un’alternativa».
Se il sodio è obsoleto, va da sé che il piombo sia paleolitico. Almeno a giudicare dalle differenze prestazionali, di efficienza (75% rispetto a 96%), e in termini di cicli di ricarica (1.000 rispetto a 4.000), come ci ricorda il sito di Flash Battery. Lo slancio comparativo investe anche la media ponderata delle batterie al litio concorrenti: la ricarica al 50% è stimata in 25 minuti rispetto all’ora, senza considerare l’azzeramento del fermo macchina. A proposito di downtime, efficienza e carica, Righi ci descrive la genesi del bilanciamento elettronico concepito e sviluppato della società reggiana.
«È partito dall’idea di realizzare qualcosa di diverso per supportare la chimica Lfp, che tendenzialmente presenta delle differenze importanti tra una cella e l’altra e, avendo una curva piatta, eroga la stessa tensione da 0 a 95%. Insomma, si fatica a bilanciare durante il funzionamento del veicolo, a differenza della Nmc. Abbiamo pertanto creato questo sistema che presenta una potenza superiore, ci consente di aggiungere e togliere energia da ogni singola cella, ed è venti volte più potente di un tradizionale battery management system. In questo modo siamo riusciti ad ottenere dei fine carica molto più veloci, meno di mezzora. Si rivela provvidenziale per gli operatori professionali: se si fanno più cicli, i costruttori tradizionali ti impongono una carica completa alla settimana e di lasciare il veicolo fermo per almeno otto ore. Noi garantiamo un utilizzo continuativo, con uno stop indicativamente di 30 minuti ogni 3 settimane. Supportiamo le celle più basse anche in scarica».
Giuseppe Corcione, ad di Reinova, in una recente intervista ha individuato nella gestione software il vero divario competitivo dell’industria europea. Qual è la ricetta di Flash Battery?
«Facciamo tutto internamente, il che facilita l’aggiornamento continuo. Stiamo introducendo un cloud sempre più intelligente che capisce in maniera chiara il vero “state of health” delle batterie. Ricevendo un maggior numero di informazioni lato cloud, riusciamo a lavorare con algoritmi di machine learning e intelligenza artificiale, che stiamo ribaltando all’interno del Bms stesso. Prima si sono affinati gli algoritmi nel Flash Data Center (il nostro software proprietario di controllo da remoto), adesso li stiamo riportando a livello macchina. Le nostre batterie utilizzano aggiornamenti over-the-air, che ci consentono di verificare il funzionamento e intervenire da remoto, migliorando il funzionamento delle batterie man mano che il tempo passa. È fondamentale, perché la batteria è un elemento deperibile. Se mi accorgo tardivamente di un cattivo funzionamento, non è possibile correre ai ripari, devo per forza di cose sostituirla. Ci avvaliamo dei gemelli digitali. Il sistema elabora una stima e, se qualcosa non va nel verso giusto, si interviene subito, senza aspettare il fine vita».
La densità di potenza è il comune denominatore di endotermici e Bev. Dal vostro lato, come si raggiunge questo obiettivo?
«Nel nostro settore, si parla di densità di energia più che densità di potenza. Le applicazioni richiedono che sia erogata un’energia costante più che dei picchi di potenza. La partenza è sempre la cella. Nella miniaturizzazione del pacco batteria, ciò che fa la differenza è migliorare la densità energetica della cella, almeno nella misura preponderante dell’obiettivo. Per la parte residuale, bisogna spingere sull’efficienza nella composizione della batteria stessa: come la assemblo e comprimo le dimensioni dell’elettronica di controllo, dei dispositivi di sicurezza e di tutto il resto. Ci rivolgiamo ai più importanti fornitori di celle, per garantire continuità di approvvigionamento. Dalla cella in avanti, ci siamo attrezzati per avere il controllo in casa. Abbiamo fatto un investimento importante installando una linea di assemblaggio automatizzata con saldatura a laser, per creare i moduli internamente. Ci distinguiamo così da altri concorrenti, che si riforniscono dei pacchi assemblati all’origine. Siamo quindi più flessibili nel customizzare i moduli e variamo agevolmente il fornitore in caso di anomalie nella catena di approvvigionamento».
Qual è lo spettro reale di ricarica in base al ciclo di lavoro di una macchina? I cicli di carico-scarico e l’autonomia soffrono delle variabili ambientali. Come intervenite per limitare l’entropia dovuta al rigore invernale?
«Le batterie sono dotate di termoregolazioni, bisogna scaldarle in presenza di climi rigidi. In questi contesti sono peraltro abituati a riscaldare anche i veicoli endotermici, per garantire la massima operatività. In base alle performance richieste l’utilizzatore di un veicolo elettrico deve attendere che le batterie siano in temperatura, quando ci si trova sottozero. A meno dieci, una batteria funziona comunque, sebbene non si possa esigere fin da subito la massima potenza. Anche in questo caso, è sufficiente lasciarla collegata. Il raffreddamento è meno nevralgico di quanto avviene nel mondo automotive, perché sulle applicazioni industriali la batteria si scarica in diverse ore e anche la ricarica non è super veloce, dal momento che il limite non è la tecnologia, ma la fonte, cioè dove effettuo la ricarica. Nei depositi del “last mile delivery”, avviene spesso con potenze non superiori a 6 chilowatt sulla singola presa. I punti di collegamento sono il collo di bottiglia. Le batterie non si scaldano perché mediamente la ricarica richiede da due a sei ore, invalidando la necessità del raffreddamento. I cantieri vanno nella direzione degli accumuli, che fungono da buffer e si occupano anche delle varie utenze».
La Motor Valley è diventata sorprendentemente un focolaio attivo di specialisti dell’elettrificazione.
«L’Emilia-Romagna è sempre stata all’avanguardia nell’elettrificazione e ne sta portando a casa i frutti. Fin dai suoi primi vagiti, Zapi ha supportato il mondo del carrello elevatore, pioniere assoluto nell’elettrificazione. Collaboriamo con tutti, gli altri attori della catena di fornitura sono potenziali partner, per offrire la soluzione corretta al cliente. Ci rivolgiamo ai produttori di macchine europei, con la consulenza di aziende che fanno da system integrator. In Italia lo facciamo direttamente, perché non abbiamo bisogno di intermediari. C’è sempre stata collaborazione in questa filiera. I nostri interlocutori d’oltralpe fanno shopping nella nostra zona, quando elettrificano una macchina».
È fattibile una collaborazione con altri costruttori per confezionare una driveline completa?
«Ufficiosamente è così, ci scambiamo informazioni per interagire mediante prodotti tra di loro complementari. È nell’interesse di tutti che i nostri clienti limitino al massimo gli sforzi e vedano i fornitori il più possibile integrati. Batterie e controllo motore sono prodotti strettamente collegati, più di quanto avvenga, ovviamente, con il motore».
La customizzazione: in che termini?
«Flash Battery dispone di un ufficio tecnico diviso in due sezioni: una che si occupa di moduli standard e un altro gruppo di lavoro che crea la batteria su misura per il cliente, partendo da questi moduli standard. L’attività di customizzazione scaturisce dalla consulenza iniziale. Ci adoperiamo per integrare all’interno della batteria i componenti richiesti dagli installatori, per fornire un servizio aggiuntivo al cliente. La batteria potrebbe diventare una Pdu (Power distribution unit) e integrare diverse uscite e diversi ingressi per ottimizzare l’installazione sul veicolo stesso».
L’industria automotive europea è sull’orlo di una crisi di nervi. Questa impasse, e la claudicante transizione energetica, possono incidere sulla democratizzazione dei consumi e riverberarsi negativamente sui costi della componentistica per l’off-higway? Gli investimenti nell’elettrico sono però troppo massicci, oserei dire “compromettenti” per lo stato di salute di Oem e solution provider, per riavvolgere il nastro come nulla fosse. Voi come la vedete?
«Il mondo dell’industria deve essere guidato dalla ricerca dell’efficienza. Non si può mettere in discussione la trazione elettrica, la combinazione inverter e motore riesce a superare il 97% di efficienza. Non esiste un’altra strada. Ovvio che non può essere “on/off”, serve a tutti il tempo di capire come procedere in questa direzione: per gli Oem, cosa fare, per i dealer, come vendere, per i clienti, capire come utilizzare queste tecnologie. Serve tempo per digerire questa soluzione. La diffusione nell’automotive sta giovando all’off-highway, perché i prezzi si sono decisamente abbattuti, rispetto ad anni fa. Più si aumentano i volumi, più si avranno veicoli con una differenza minore tra termici ed elettrici».
Per leggere l’articolo completo clicca qui oppure scarica il pdf.