Fpt Industrial. Tra assali e trasmissioni
Fpt Industrial alle prese anche con assali e trasmissioni per camion e autobus Tutto ha inizio dalla joint venture tra Iveco e Rockwell che coincide con l’inizio della storia degli assali Iveco. Stiamo parlando dei gloriosi anni ’70 e dovremo invece attendere il 1991 per vedere la nascita dell’anima drivetrain di Fpt Industrial a Torino. […]
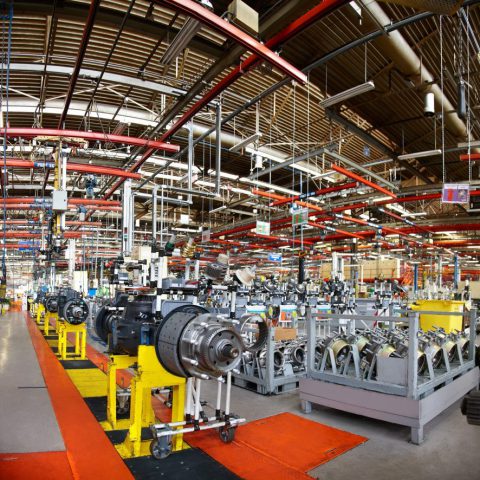
Fpt Industrial alle prese anche con assali e trasmissioni per camion e autobus
Tutto ha inizio dalla joint venture tra Iveco e Rockwell che coincide con l’inizio della storia degli assali Iveco. Stiamo parlando dei gloriosi anni ’70 e dovremo invece attendere il 1991 per vedere la nascita dell’anima drivetrain di Fpt Industrial a Torino. Proprio in questa città abbiamo visto l’ascesa di assali e trasmissioni per camion e autobus.
Tre linee di cambi manuali: 2850.6, 2840.6 e 2835.6, in grado di gestire coppie da 200 a 500 Nm, modulando la trasmissione in base alla coppia motrice e ai rapporti dell’applicazione. Il tutto ha origine dalla collaborazione con Interpump. La parola d’ordine è: efficienza. L’obiettivo, oltre ad avere un basso total cost of ownership ed una durata consistente, è quello di ridurre il rumore, fattore cruciale per alcune tipologie di applicazioni, come i minibus.
Per trovare una soluzione interviene la cella semi-aenecoica. Al suo interno si svolgono analisi acustiche secondo gli standard Iso, per consentire la replicabilità e la comparabilità degli spettri sonori. Si tratta di una camera di ultima generazione, dove le pareti a cuneo sono state sostituite da pannelli fonoassorbenti.
La fase di problem solving interviene quando un motore o una trasmissione manifesta una certa rumorosità e la soluzione viene da un’analisi spettrale e algoritmi specifici per individuare difetti e anomalie.
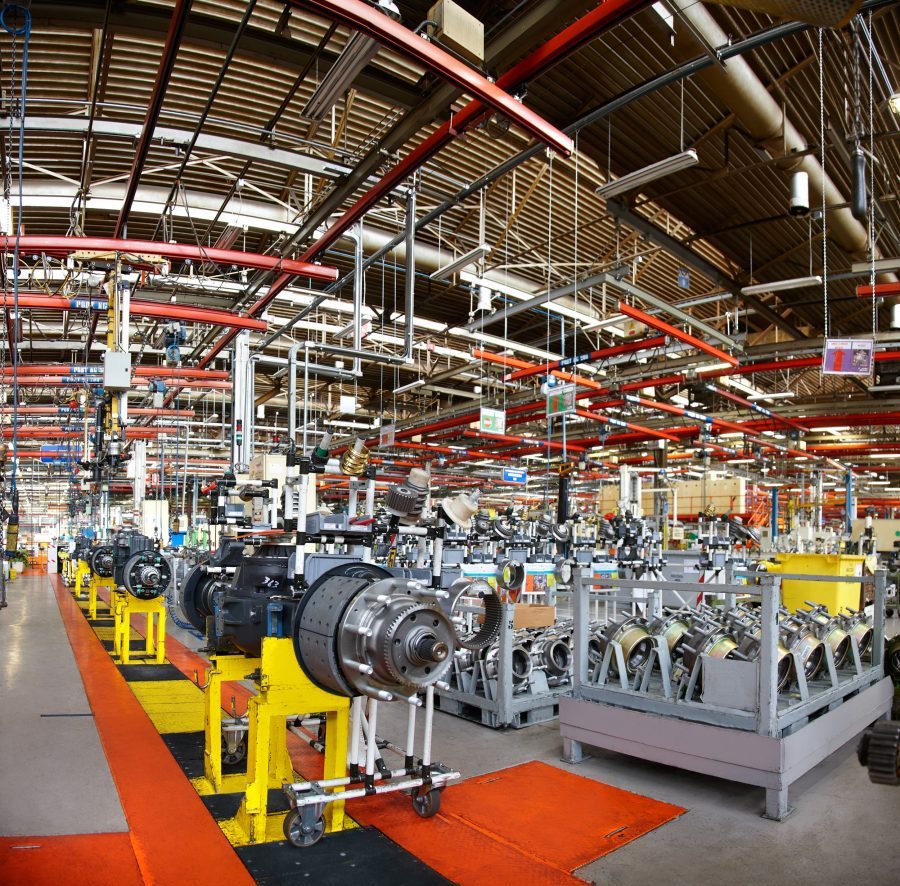
Efficienza e innovazione sono sicuramente presenti
Gli assali rigidi sterzanti tollerano un carico da 3,6 a 18 tonnellate, 30 kNm di coppia frenante e supportano veicoli fino a 40 ton. I ponti sono disponibili sia con riduzione singola che con doppia riduzione e supportano un peso massimo tra 2 e 40 tonnellate e utilizzano freni a disco dal 2017, aumentando l’efficienza del 2 per cento.
La lavorazione dei fusi è stata rinnovata tra il 2017 e il 2018 ed è stata sviluppata da zero una linea automatica per la lavorazione (con centri di lavorazione di ultima generazione ispirati a concetti di industria 4.0, incluso il monitoraggio dei parametri fondamentali sul pc dell’operatore), oltre ad una nuova linea di assemblaggio (che segue i principi di golden zone material, minimum material handling, trasporti automatici).
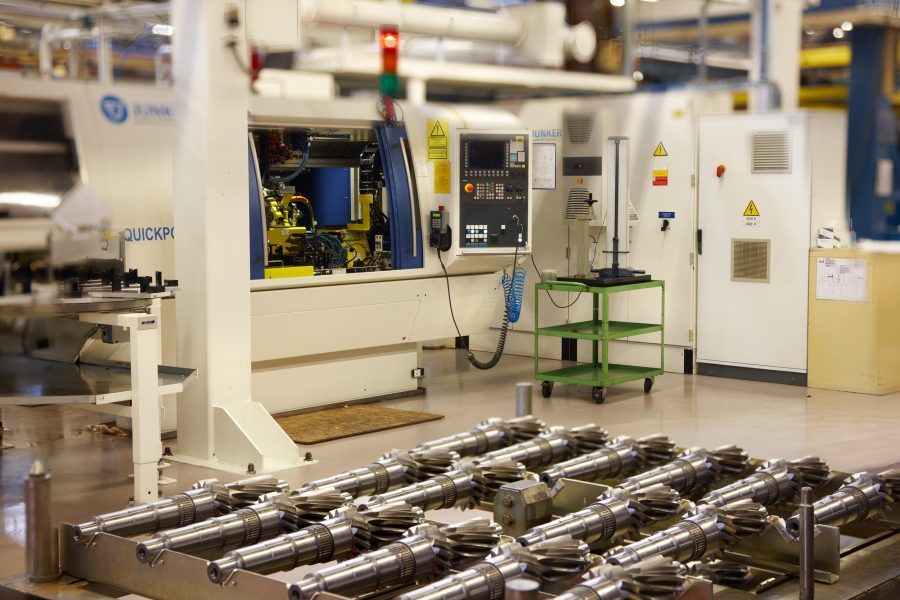
Nel 2017, non c’è stata soltanto l’introduzione dei freni a disco e della rivoluzione X-Way. C’è stata anche la fine della lubrificazione, con l’aggiunta di un cuscinetto per ogni ruota.
Il software X-Way è in grado di utilizzare la matrice di efficienza, calcolata secondo la procedura Acea, per determinare l’efficienza globale del veicolo.