Fraunhofer Ise: prima sintesi di metanolo dal gas di altoforno
Il metanolo è attualmente considerato uno dei principali vettori energetici nella nascente economia dell’idrogeno. Tuttavia, la produzione convenzionale di metanolo da carbone e gas naturale genera grandi quantità di emissioni di gas serra. Con il progetto “Carbon2Chem”, per la prima volta, in un mini impianto Fraunhofer Ise è stata dimostrata per la prima volta la stabilità a lungo termine della sintesi del metanolo dal gas d’altoforno purificato.
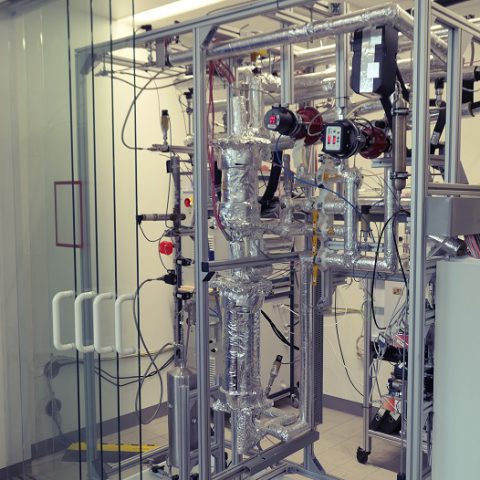
Il metanolo svolge un ruolo importante per l’industria come sostanza chimica di base ed è attualmente considerato uno dei principali vettori energetici nella nascente economia dell’idrogeno. Tuttavia, la produzione convenzionale di metanolo da carbone e gas naturale genera grandi quantità di emissioni di gas serra. Con il progetto “Carbon2Chem”, i partner dell’industria, della ricerca e del mondo accademico hanno deciso di esplorare i processi per la produzione di metanolo dai gas di scarico industriali, prendendo come esempio l’industria siderurgica. Per la prima volta, in un mini impianto Fraunhofer Ise con una capacità di produzione di dieci litri al giorno per un totale di oltre 5.000 ore, è stata dimostrata per la prima volta la stabilità a lungo termine della sintesi del metanolo dal gas d’altoforno purificato effettivo. Nel 2018, thyssenkrupp ha fornito la prova di concetto per la produzione di metanolo dal gas di altoforno nell’ambito di questo progetto.
La sintesi di metanolo fossile e la produzione di acciaio tramite il percorso dell’altoforno a base di carbone sono responsabili di significative emissioni di CO2 di gas serra. Il collegamento dei due processi consente di sostituire il metanolo dai combustibili puramente fossili facendo reagire l’idrogeno verde con le emissioni della produzione di acciaio. “Gli impegni previsti dall’accordo di Parigi sul clima possono essere rispettati solo collegando i settori industriali. Dobbiamo portare in un ciclo le emissioni difficili da evitare”, spiega Achim Schaadt, capo del dipartimento dei processi termochimici presso Fraunhofer Ise.
Il progetto Carbon2Chem, lanciato nel 2016 e finanziato dal Ministero federale tedesco dell’istruzione e della ricerca, sta sperimentando processi per convertire i gas di processo dell’industria siderurgica in prodotti chimici di base. “In Carbon2Chem, le forze innovative dell’industria, della ricerca applicata e delle università si uniscono per raggiungere rapidamente una soluzione globale implementabile e ottimizzata dal punto di vista sistemico”, sottolinea Luis F. Piedra-Garza di thyssenkrupp Steel Europe.
Gas di scarico come condotti
Fraunhofer Ise, che da dieci anni lavora nel campo della sintesi del metanolo, si è affidato a un concetto di elaborazione semplice e robusto per lo sviluppo del mini impianto. Si basa su due reattori adiabatici non raffreddati e un riciclo di tipo industriale dei gas non reagiti. L’impianto è entrato in esercizio di prova con gas in bombola presso il Fraunhofer Ise di Friburgo nel 2017 prima di essere trasferito all’impianto pilota Carbon2Chem di Duisburg nel 2019. I gas di scarico della vicina acciaieria integrata sono trattati in un sistema di purificazione del gas di thyssenkrupp Industrial Solutions utilizzando catalizzatori e assorbenti dell’azienda chimica specializzata Clariant e sono privi di veleni catalizzatori per la successiva sintesi. “Il personale di thyssenkrupp Uhde Engineering Services mantiene il sistema di pulizia del gas in funzione 24 ore su 24. L’acciaieria opera su tre turni, quindi c’è sempre abbastanza gas. Abbiamo quindi le condizioni ideali per il funzionamento continuo su scala di un impianto pilota”, spiega Max Hadrich, capo del gruppo Power to Liquids presso Fraunhofer Ise.
In un totale di oltre 5.000 ore di funzionamento in loco, sono stati prodotti oltre 1.500 litri di metanolo grezzo. L’obiettivo era quello di utilizzare il gas purificato d’altoforno, che rappresenta la quota maggiore, l’85%, dei gas di acciaieria. In un test a lungo termine della durata di oltre 3.000 ore, non è stato rilevato alcun calo significativo dell’attività del catalizzatore. Ciò attesta il buon funzionamento del catalizzatore e la progettazione dell’impianto. “Carbon2Chem e la collaborazione con Fraunhofer Ise forniscono un quadro ideale per sottolineare le prestazioni dei nostri catalizzatori industriali di sintesi di metanolo MegaMax per la conversione efficiente e stabile di gas di processo ricchi di CO2”, commenta Andreas Geisbauer del partner di progetto Clariant.
Ottimizzazione dei processi con il gemello digitale
Un importante prerequisito per l’ottimizzazione del processo di sintesi del metanolo dal gas di sintesi ricco di CO2 è il miglioramento del modello cinetico per il catalizzatore Clariant utilizzato in Carbon2Chem, poiché le reazioni con un ciclo di riciclo come la sintesi del metanolo richiedono una profonda comprensione delle complesse interazioni del parametri di processo. Sulla base del modello cinetico migliorato sviluppato internamente, Fraunhofer Ise è stato in grado di creare un gemello digitale del mini impianto. Ciò consente di accelerare i processi di apprendimento riducendo al minimo i rischi di scale-up per i futuri impianti industriali: “Dopo aver convalidato i nostri modelli con i dati del miniimpianto, siamo stati in grado di simulare e ottimizzare i parametri dell’impianto. Utilizzando i risultati della simulazione, siamo riusciti ad aumentare passo dopo passo le prestazioni del miniimpianto”, riferisce Florian Nestler, ricercatore associato presso Fraunhofer Ise.
Concetto di controllo per la dinamica dell’acciaieria integrata
I gas di acciaieria sono una materia prima essenziale per l’impianto, ma non sono costanti nella loro quantità e composizione. Questa condizione al contorno, che si verifica frequentemente per i processi basati su fonti di energia rinnovabili fluttuanti, è una nuova sfida per la sintesi del metanolo. A seconda delle condizioni operative o delle materie prime disponibili, le proprietà dei gas della cokeria, dell’altoforno (conversione del minerale di ferro in ghisa) o del convertitore (conversione della ghisa in acciaio) possono variare considerevolmente. Con i dati raccolti, è ora possibile progettare un concetto di controllo per rispondere ai cambiamenti in tempo reale e mantenere la sintesi in un punto operativo ottimale in ogni momento.
“Siamo lieti di aver completato con successo le prove a Duisburg e di poterci dedicare all’ampliamento del processo”, afferma Max Hadrich. I modelli di processo convalidati verranno utilizzati in una fase successiva per progettare impianti su larga scala, effettuare valutazioni tecnico-economiche e valutare l’impronta di CO2 del processo.