Liebherr D9812 and Kohler SDMO
Liebherr and Kohler. Born for Liebherr mining applications, grew up as a genset for Kohler SDMO, D9812 is developing the strong identity of a polyhedral and efficient industrial engine for the free market heavy-duty applications. In the previous articles, our readers got to know the winner of the “Diesel of Year 2017” award, the D9812, […]
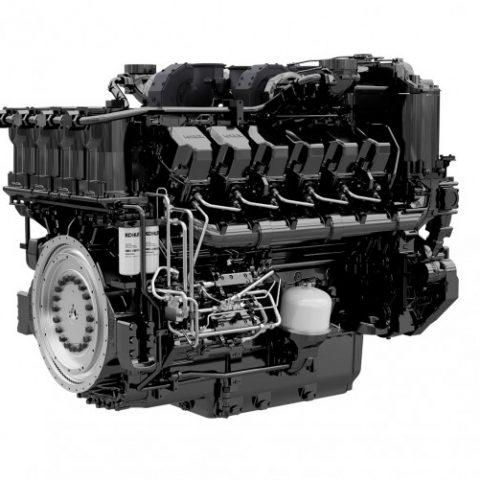

Liebherr and Kohler. Born for Liebherr mining applications, grew up as a genset for Kohler SDMO, D9812 is developing the strong identity of a polyhedral and efficient industrial engine for the free market heavy-duty applications. In the previous articles, our readers got to know the winner of the “Diesel of Year 2017” award, the D9812, by Liebherr better. Further variants of this engine have already been designed. In our last article, we gave you more information about the mining configuration of this engine, for example for hauling trucks and hydraulic excavators.
READ MORE ABOUT THE ‘HIDDEN ORGANIZER’ OF QUARRIES AND MINES
Liebherr and Kohler: the big heart of a Genset
In addition to this mining variant, a Genset configuration of the D98XX series is already available and in serial production. Therefore, we would like to devote this issue to the details of the power generation variant of the D9812, which is the result of mutual expertise and collaboration on behalf of Liebherr and Kohler.

Liebherr and Kohler: a 360° partnership
As a global force in power solutions since 1920, Kohler has been committed to reliable, intelligent products, purposeful engineering and responsive after-sale support. Kohler’s acquisition of SDMO Industries in 2005 gave birth to the world’s 3rd largest manufacturer of industrial generators. Kohler delivers integrated industrial power systems for emergency, prime and continuous applications worldwide — from data centers and hospitals to water treatment facilities and government offices. Liebherr’s 30 years of experience in the manufacturing of engines now goes together with the expertise by Kohler. Together, the two companies have co-developed the K175 engine series, which corresponds to the G Drive version of the D98XX series. A significant detail of the cooperation between Liebherr and Kohler: these G-Drive engines exclusively power the recently-launched KD Series of KOHLER and KOHLER-SDMO diesel industrial generators.
Liebherr and Kohler in the sign of power density
The KD62V12 G-Drive diesel engine, which is the 12 cylinder variant of the K175 series, offers outstanding specific power in a clean and modular design. Created specifically for generator set applications, this new engine is combining greater power with superior efficiency. Reaching up to 43.5 kW/liter, the G-Drive engine pairs a compact form factor with unrivaled kW displacement, thus delivering the highest power density in the market. In fact, the G-Drive engine produces industry leading kW displacement in a package that enables a smaller generator set footprint while delivering the best fuel consumption. That means higher performance at reduced operating cost. The engine architecture, injection system and engine management of G-Drive engines have been designed to achieve optimal generator set performance, while meeting all worldwide emission requirements.
POWER DENSITY? ONE OF THE REASONS TO BE DIESEL OF THE YEAR 2017…
Liebherr and Kohler optimize turbo charger system
The unique turbocharger system optimizes the airflow to the cylinders for maximum power, optimal combustion as well as reduced fuel consumption. Moreover, the low-noise combustion system with optimized pressure works in combination with a rigid engine block, crankcase and sub-frame to significantly reduce noise and vibration. The G-Drive engine has been purposefully designed for long-life performance inside the KOHLER® or SDMO® generator—power systems that are backed by a three-year emergency standby power (ESP) warranty.
Low operating and maintenance costs
Costs to operate and maintain this G-Drive engine are reduced through low fuel consumption, increased power density, reduced acquisition costs and diagnostics that help to prevent issues. The innovative fuel system by Liebherr with common rail injection, which reaches pressures up to 2200 bar, helps to deliver a better atomisation of fuel and improved fuel consumption. This precisely-metered fuel injection system also minimises fuel return, engine particulates, reduces emissions and helps the new engines to meet global emission regulations in all markets. Unlike other common rail systems, this engine is not using returned fuel to cool the engine.
THE IMPORTANCE TO BE ‘DRIVEN’ BY A LIEBHERR COMMON RAIL
That means the minimal fuel being returned is at ambient temperature, a nice advantage for the KD Series engine when developing industrial power systems. As a conclusion, with its high power density and its robust and reliable design, the Genset variant of the D9812 engine, the KD62V12, is the new reference for the power generation applications, be it emergency, prime or continuous applications.