Liebherr D9812 common rail
Liebherr D9812 is equipped by its own common rail Liebherr is well known as a supplier of construction machinery, but also as a manufacturer of a huge variety of components, among them diesel and gas engines, hydraulic pumps and motors, switchgear and electronics. All components are developed and produced in-house. The Liebherr injection system development […]
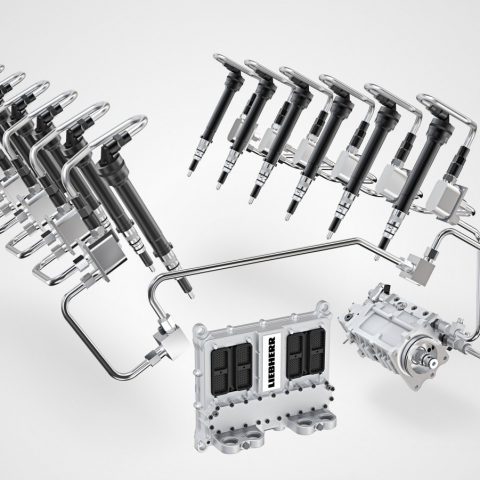
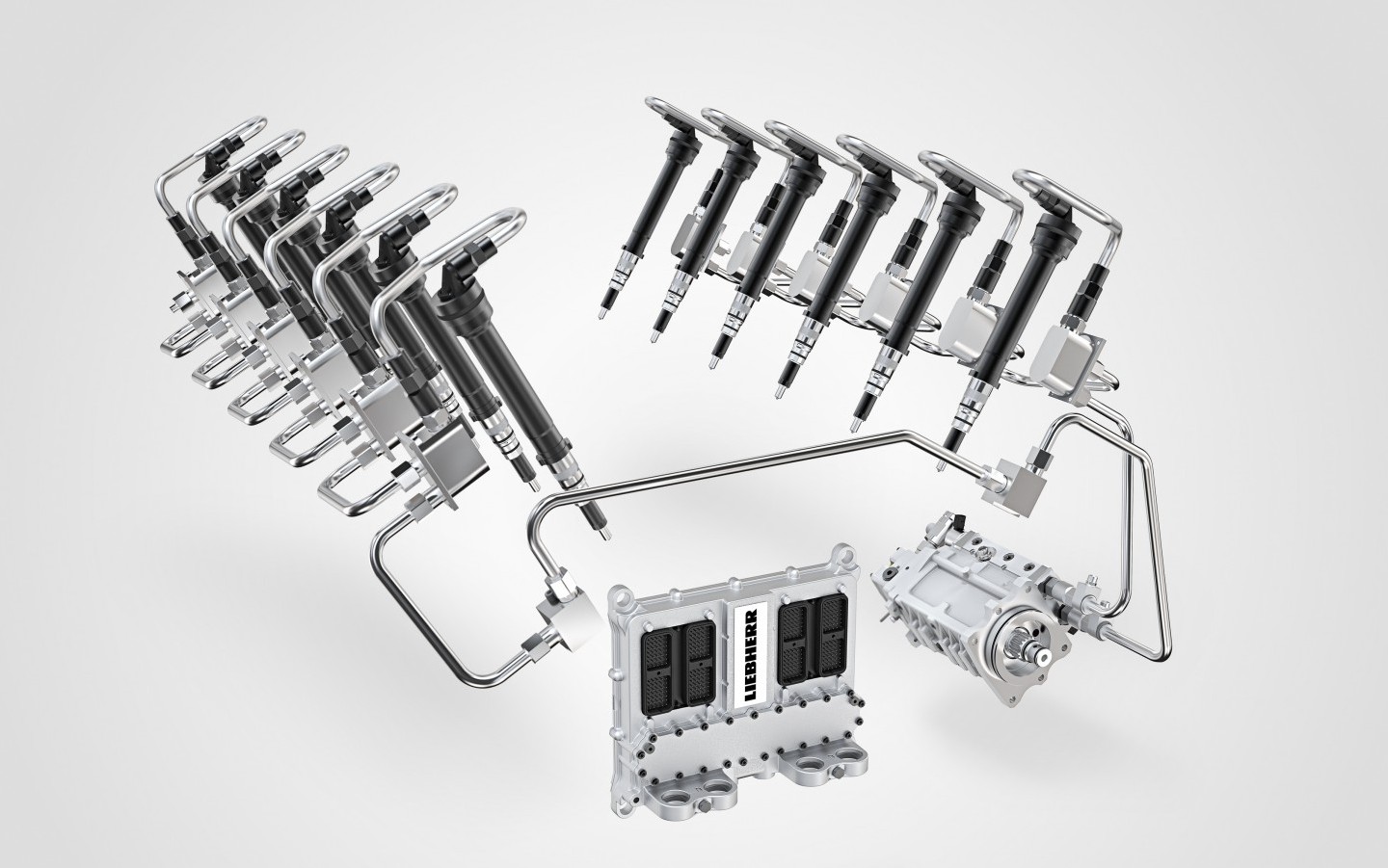
Liebherr D9812 is equipped by its own common rail
Liebherr is well known as a supplier of construction machinery, but also as a manufacturer of a huge variety of components, among them diesel and gas engines, hydraulic pumps and motors, switchgear and electronics. All components are developed and produced in-house. The Liebherr injection system development is a good example of this approach.
Since 2012, Liebherr has manufactured its own common rail system, consisting of the LP11.2 high pressure pump and the LI2.7 injector, later on followed by the new pump LP11.5 and injector LI3.13 for high power engines. This new common rail system fits engines with up to 5.17 l/cylinder such as the D9812, the winner of Diesel of the Year 2017, and engines having a max. power of 4.5 MW. The injector nozzle flow rate can be individually adapted between 1,600 and 4,000 ml/30sec@dp=100bar, depending on the specific application; the injectors have an integrated fuel accumulator and are driven by a HD-ECU for up to 12 cylinders. The 5-plunger pump delivers up to 825 l/h @ 2,200 bar.
Coming to components, the LI3.13 injector features the same layout, including the 3-way valve technology, of the previous LI2.7 injector, it is permanently leakage free and provides high hydraulic efficiency. Differences are mainly based on integration of the pressure accumulator into the injector body and the, therefore, different structure of the injector itself. The fuel enters on the top of the injector, passes a laser bored filter with very low pressure drop and enters the pressure accumulator. To connect the accumulator to the needle housing, three or six coaxial bores are crossing the magnet housing and are leading into the needle housing. The scope of the design is focused on maximum avoidance of potential pressure drops to achieve a maximum efficiency of the overall injection system.
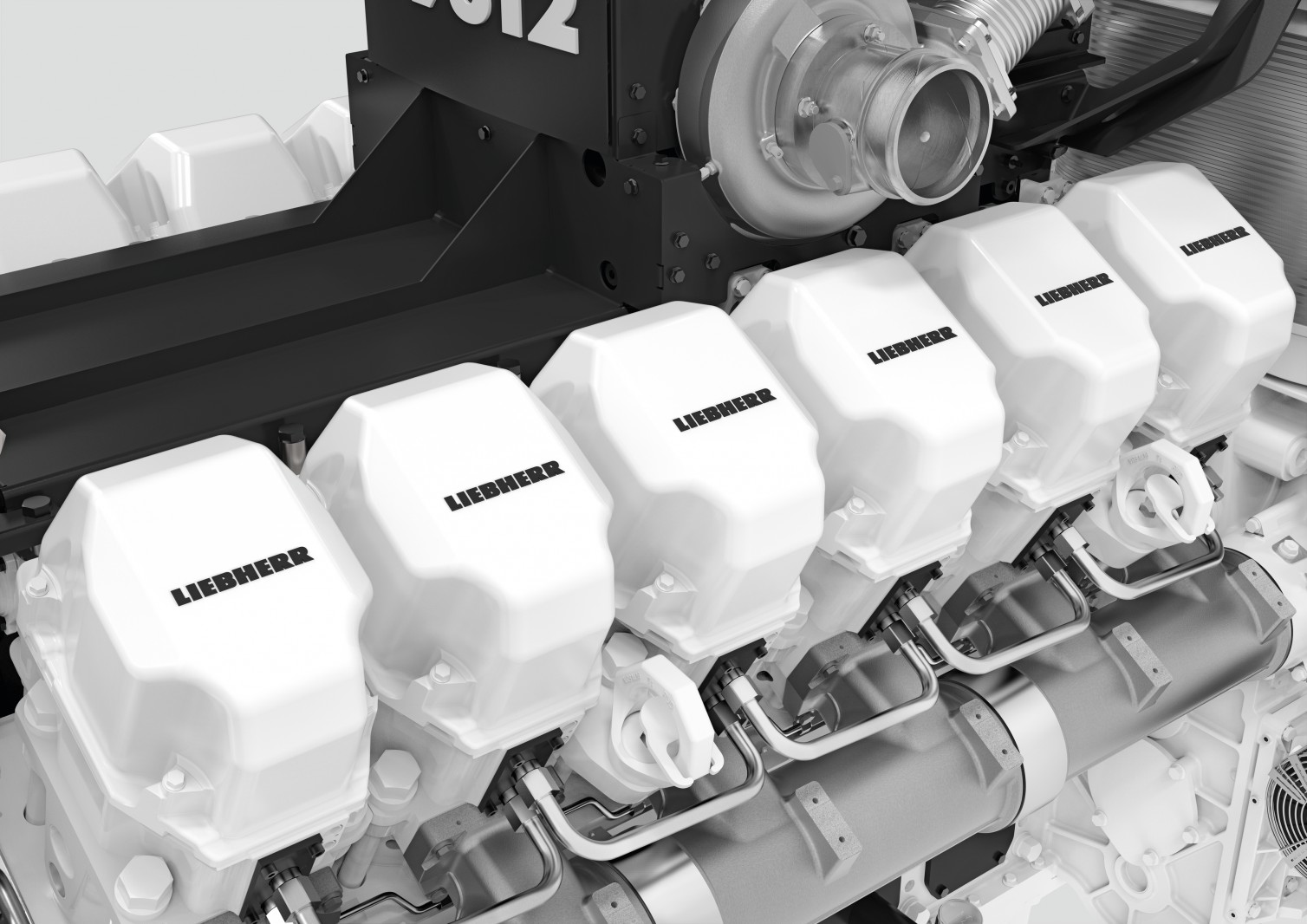
3-way valve
Needle opening and closing are controlled by a new improved 3-way valve. The high pressure pump LP11.5 also is a direct offshoot of the smaller pump LP11.2. In order to avoid interaction between the cylinders due to elastic deformation during the pumping events, the cylinder axes of neighbouring cylinders were inclined by 7.5° to each side. Thanks to this relatively small angle, the pump is much shorter than a conventional inline pump, but not as wide as a conventional V-pump. In consequence, crankshaft, bearings and crankcase of the pump are also thinner and weight-optimised without losing stiffness. The pump features two rails with four connecting positions. All four interfaces for the high pressure pipe connection are machined identically, so it is possible to choose the piping position depending on engine layout. The eccentrical principle of the pump drive in combination with oil lubrication leads to a very high robustness of the pump. Another important benefit of the eccentric drive is the very low peak torque during operation (only 180 Nm).
Liebherr offers three different types of engine control units for its fuel injection systems: a compact ECU for on- & off-highway engines with up to 6 cylinders (ECU3) and two highly robust off-highway ECUs for engines up to 8 (ECU2) or 12 and more cylinders (ECU2-HD).
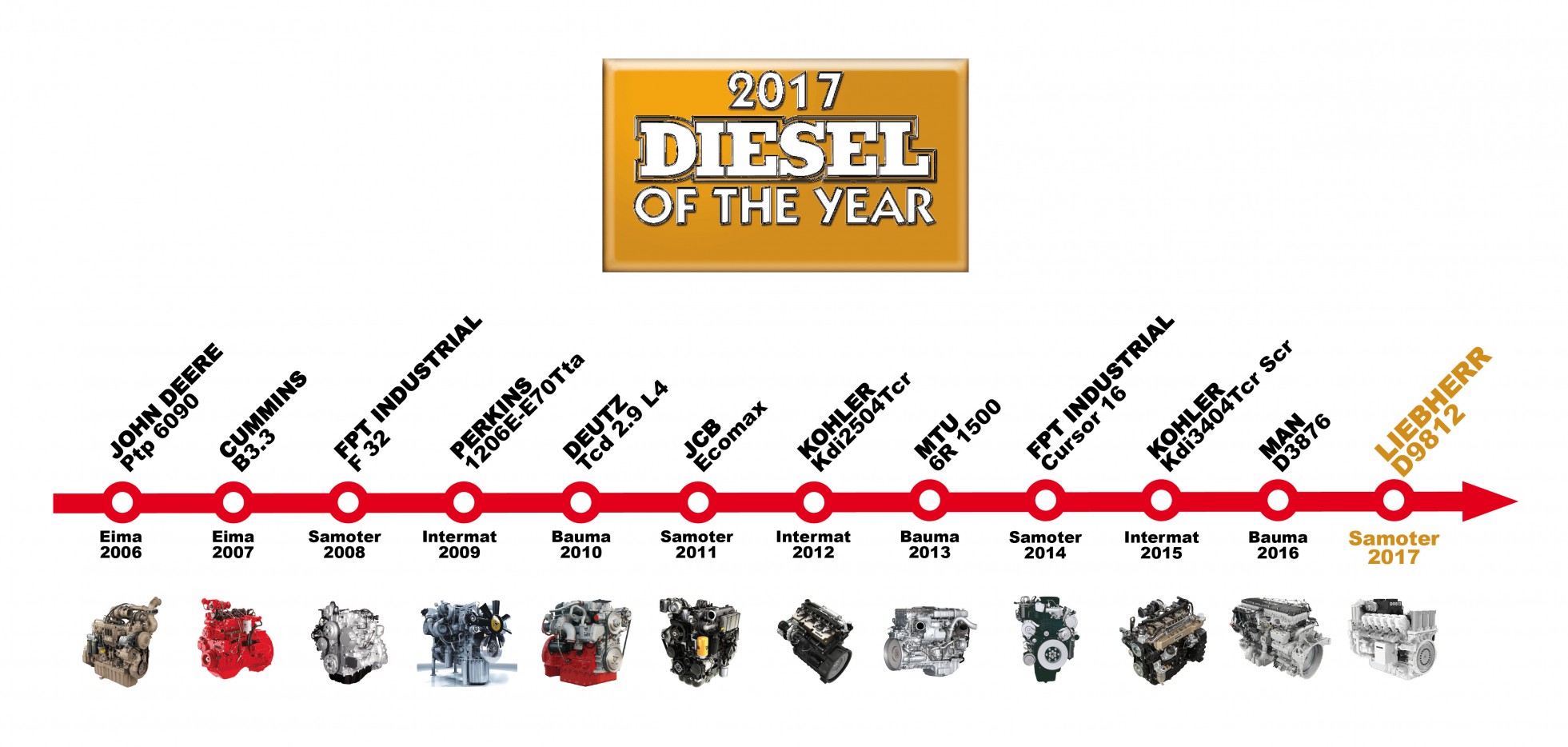