Da Ricardo una spinta alla digitalizzazione. Machine learning, mai più senza
Strumenti e tecniche resi possibili dallo sviluppo della digitalizzazione, ormai è chiaro, possono rivoluzionare l’intero ciclo di vita di un prodotto: dalla progettazione alla produzione, fino alle fasi di testing e manutenzione. Ne abbiamo parlato con gli specialisti di Ricardo.
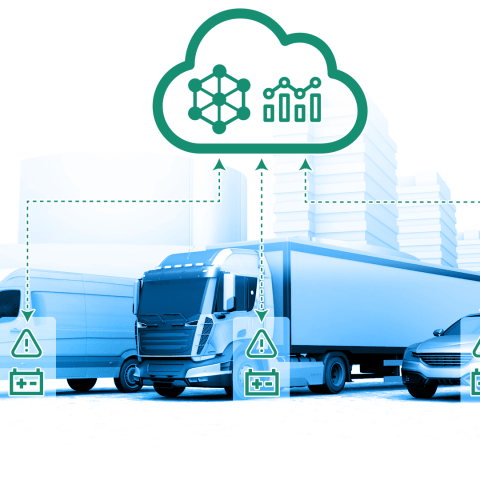
Digital twin e strumenti per lo sviluppo virtuale dei prodotti permettono di gestire la complessità dettata dall’evoluzione del powertrain, nell’automotive e non solo, per cui le tradizionali tecniche di progettazione non bastano più. Per Ricardo, l’applicazione del machine learning è cruciale per districarsi tra dati e informazioni.
Ecco a voi un estratto dell’articolo presente a pagina 32 di DIESEL Maggio
Ricardo ci spiega il machine learning
Strumenti e tecniche resi possibili dallo sviluppo della digitalizzazione, ormai è chiaro, possono rivoluzionare l’intero ciclo di vita di un prodotto: dalla progettazione alla produzione, fino alle fasi di testing e manutenzione. Questo vale sia per i veicoli con powertrain tradizionali che per veicoli ibridi o elettrici; per l’on-road e per l’off-highway, come vedremo. Con importanti distinguo da fare e, soprattutto, ben consapevoli di quali siano gli strumenti più adatti per soddisfare ogni esigenza.
Ricardo, nome di primissimo piano nella consulenza ingegneristica, ambientale e strategica, a tutto questo filone sta dedicando una serie di appuntamenti online. Ci siamo confrontati con due loro specialisti, Peter Fussey e Farraen Mohd Azmin, sull’impatto delle tecniche di machine learning e intelligenza artificiale sulla progettazione e parametrizzazione dei sistemi powertrain.
Before & after
l punto di partenza è piuttosto eloquente: nello scenario attuale è fondamentale trovare alternative virtuali a processi che si sono sempre svolti fisicamente, massimizzando al tempo stesso l’efficienza di passaggi chiave come calibrazione e validazione. Qual è, dunque, l’obiettivo che si pone Ricardo? «Aiutare le aziende a migliorare non solo lo sviluppo dei prodotti, ma anche la loro realizzazione concreta», esordisce Peter Fussey. «Le tecniche e gli strumenti che abbiamo sviluppato, infatti, sono trasversali tra i due ambiti. Automatizzare i processi comporta vantaggi tangibili e misurabili in termini non soltanto di risparmio di tempo, ma anche di qualità e affidabilità dei prodotti. Per non parlare delle ricadute positive che l’applicazione di questi principi ha sul ciclo di vita dei prodotti stessi, quindi diagnostica e prognostica di possibili problemi».

Uno scenario promettente e molto diverso se paragonato alle tecniche tradizionali. «Se prima, poniamo, lo sviluppo di un veicolo presupponeva una sequenza di azioni, test e feedback ed era fortemente dipendente dal numero di persone che lavoravano al progetto, l’automazione di tutto questo fa sì che, ora, gli algoritmi e l’applicazione di tecniche di machine learning e intelligenza artificiale siano in grado di ‘leggere’ e prevedere il lavoro che potrebbe svolgere un ingegnere, creando database alimentati da dati reali e condivisi in cloud», aggiunge Farraen Mohd Azmin.
Più nello specifico, i dati che provengono da test e dall’utilizzo reale dei veicoli vengono messi a disposizione dell’utente, che può creare modelli, mappe e fare previsioni. La costante immissione di dati porta a un accumulo di informazioni che non sarebbero gestibili senza l’ausilio degli algoritmi di machine learning, che contribuiscono a filtrare e segnalare soltanto i dati importanti e utili in una determinata fase del processo.
L’articolo completo a pagina 32 di DIESEL Maggio