Volkswagen Group dà il via al riciclo delle batterie
Pochi giorni fa a Salzgitter Volkswagen Group Components ha attivato il primo impianto del Gruppo per il riciclo delle batterie delle auto elettriche. L’obiettivo è il recupero industrializzato di materie prime preziose e di arrivare a un tasso di riciclo superiore al 90 per cento.
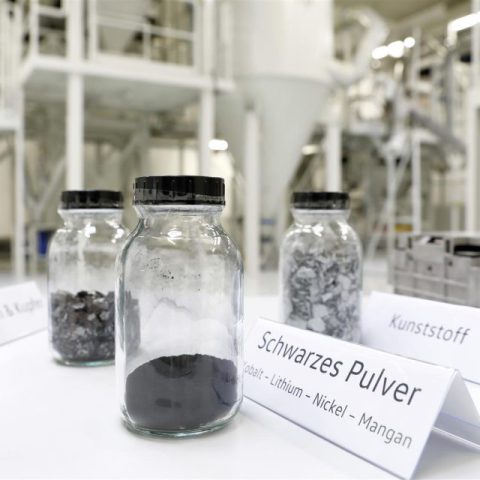
Pochi giorni fa a Salzgitter Volkswagen Group Components ha attivato il primo impianto del Gruppo per il riciclo delle batterie delle auto elettriche. Con l’avvio delle operazioni pilota, il Gruppo compie un altro coerente passo avanti verso la responsabilità sostenibile per l’intera catena del valore delle batterie per veicoli elettrici. L’obiettivo è il recupero industrializzato di materie prime preziose come litio, nichel, manganese e cobalto in un ciclo chiuso insieme ad alluminio, rame e plastiche, arrivando a un tasso di riciclo superiore al 90 per cento nel lungo termine.
La peculiarità dell’impianto di Salzgitter è che ricicla solamente batterie che non possono più essere destinate ad altri scopi. Prima di procedere con il riciclo, un’analisi stabilisce se l’accumulatore è ancora sufficientemente potente per avere una seconda vita in un sistema mobile di stoccaggio di energia, come per esempio la stazione flessibile di ricarica rapida o il robot mobile per la ricarica. Non sono previsti grandi volumi di batterie da riciclare prima della fine del decennio in corso.
L’innovativo processo di riciclo, che permette anche di risparmiare CO2, non richiede la fusione in altoforno, procedimento ad elevata intensità energetica. I singoli componenti sono ridotti in granulati nel trituratore e poi asciugati. Oltre ad alluminio, rame e plastiche, si ottiene anche la pregiata “polvere nera” (“black powder”), che contiene materie prime importanti per le batterie come litio, nichel, manganese, cobalto e grafite. La separazione e la lavorazione delle singole sostanze tramite processi idrometallurgici – utilizzando acqua e agenti chimici – viene effettuata successivamente da partner specializzati.
Spiega Mark Möller, responsabile della divisione Sviluppo Tecnico ed E-Mobility: “Le ricerche dicono che le materie prime riciclate per le batterie sono efficienti tanto quanto le nuove. In futuro vogliamo supportare la nostra produzione di celle batteria con il materiale che recuperiamo. Dato che la domanda di accumulatori e delle relative materie prime incrementerà in modo drastico, possiamo fare buon uso di ogni grammo di materiale riciclato”.
Il risparmio di CO2 calcolato è di circa 1,3 tonnellate per una batteria da 62 kWh prodotta utilizzando catodi ottenuti con materiali riciclati e usando energia elettrica da fonti rinnovabili.
Audi Battery Technology Center
Press il centro R&D di Gaimersheim, in Baviera, Audi progetta e sviluppa in-house le celle batterie ad alto voltaggio, verificando le prestazioni degli accumulatori. Nero, rosso e oro sono i colori che indicano il livello di carica di una batteria: se la cella è scarica la grafite è di colore nero, in condizioni parziali diventa rossa, a carica completa è oro. Quando un elettrodo viene caricato, ciò non avviene in modo uniforme: dove sono presenti più ioni di litio, l’elettrodo si carica più rapidamente. Il compito del centro di Gaimersheim è di far funzionare le celle agli ioni di litio in maniera ottimale, ottenendo le autonomie e le prestazioni di ricarica migliori.